QC Processes and LEAN – Driving Efficiency in Quality Control with q_alizer™
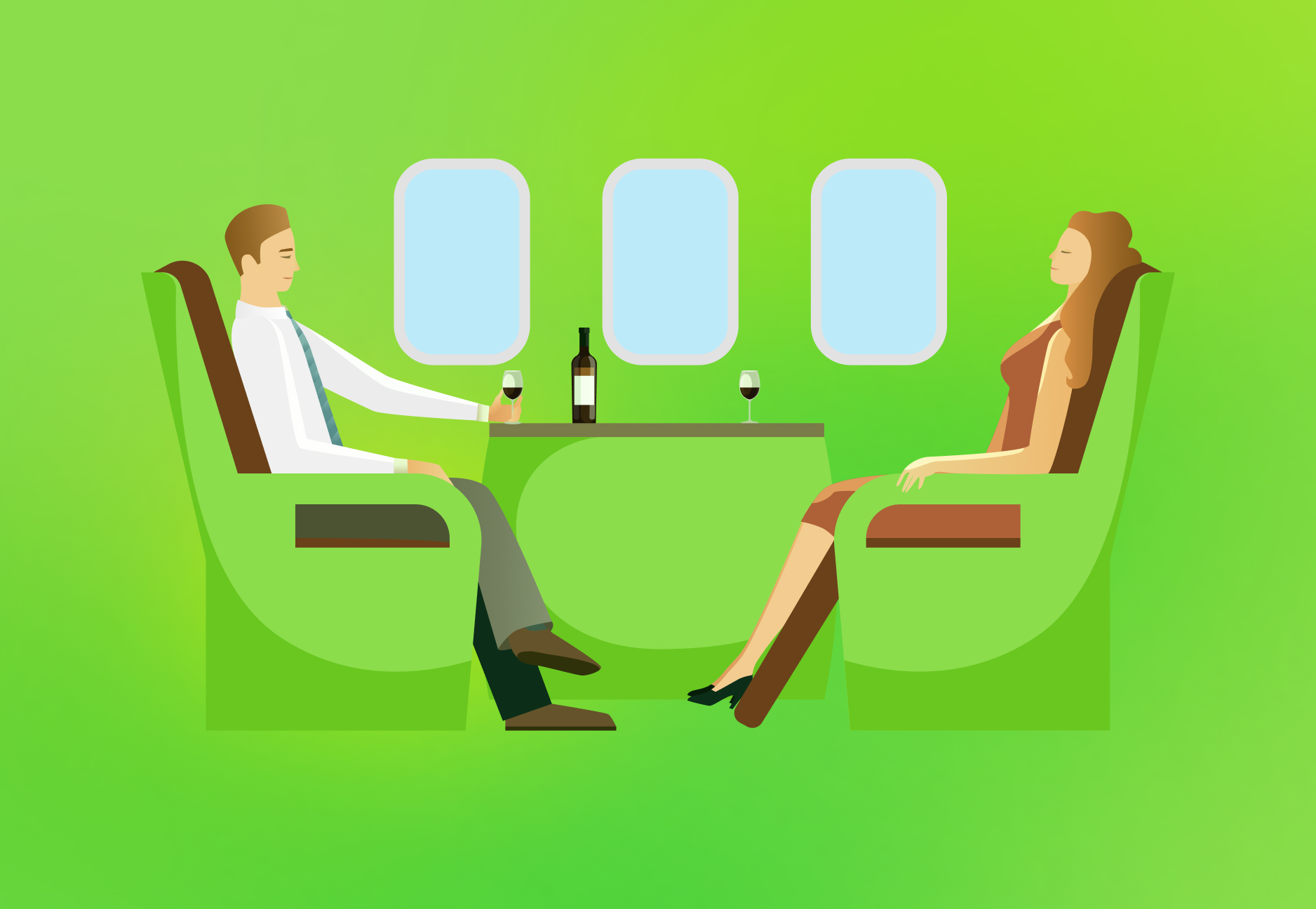
In pharmaceutical quality control, precision is vital – but so is speed. Every minute counts when it comes to batch release. Yet many labs struggle to see where time is lost, where delays build up, or which samples silently stall the process. This is where q_alizer changes the game: by making the invisible visible.
The New Imperative: Precision and Speed
In pharmaceutical quality control, precision has always been a non-negotiable standard. But in today’s environment of rising complexity and tighter timelines, speed is just as crucial. Every minute counts when it comes to releasing batches on time and managing lab resources efficiently. While LEAN principles promise a path to greater efficiency by eliminating waste and streamlining processes, the challenge remains: how do you know where time is actually lost?
Making the Invisible Visible
That’s where q_alizer comes in. Designed as a cloud-based cockpit, q_alizer doesn’t replace core systems like LIMS or MES. Instead, it integrates with them to make the performance of quality control processes fully transparent. It enables labs to analyze workflows in real time, understand where bottlenecks form, and create a measurable basis for LEAN improvement — all without disrupting daily operations.
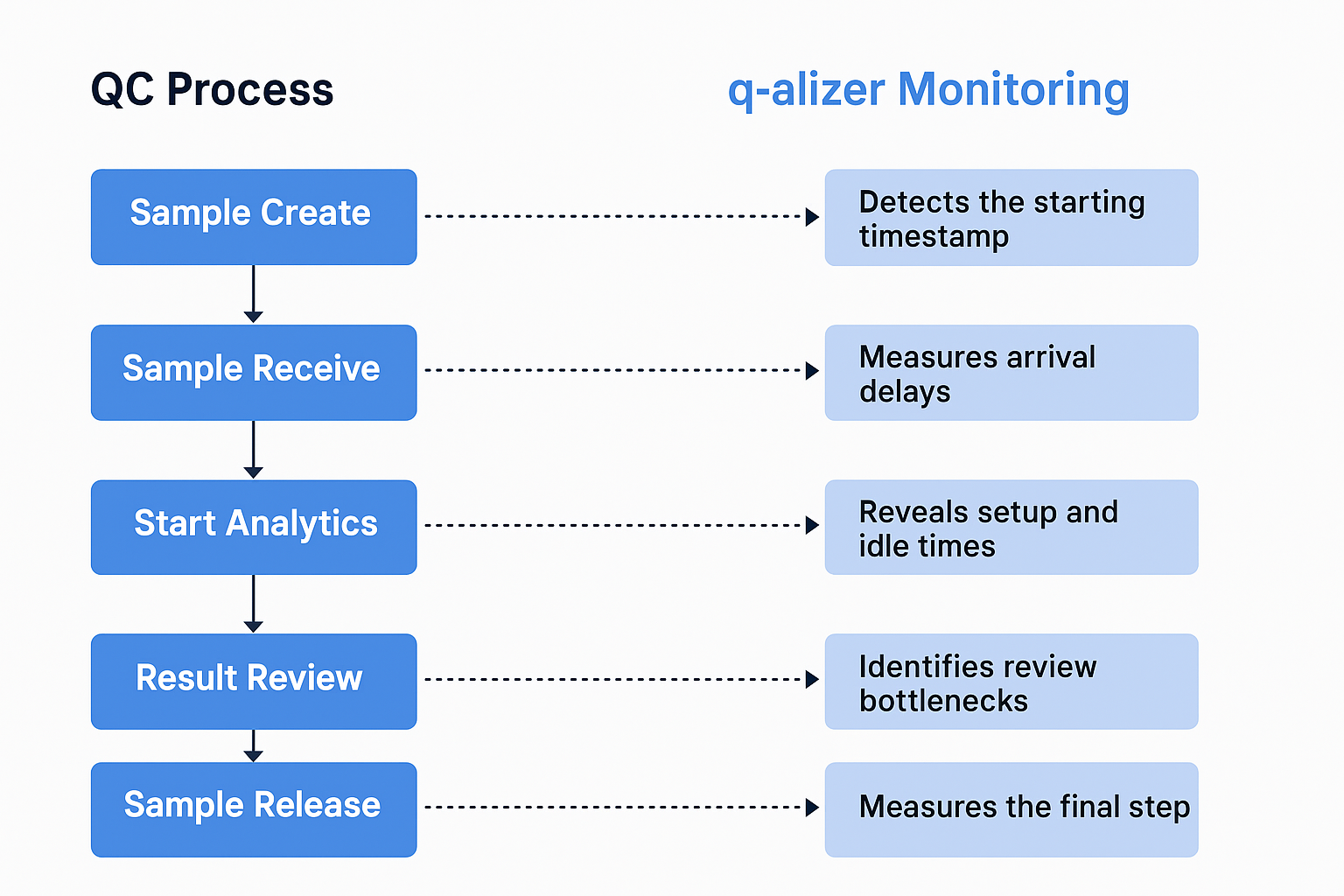
From Sample to Release: A Transparent QC Journey
Take a typical lab process, for instance. It begins when a sample is created — an event q_alizer identifies from the moment it’s registered in a system like LIMS or ERP. This creation timestamp, or “T0”, becomes the baseline for monitoring the entire sample lifecycle.
What follows is often a delay between sample creation and its physical arrival in the lab. During this time, valuable minutes — or even hours — can be lost due to transport inefficiencies or organizational gaps. q_alizer quantifies this delay, exposing issues that might otherwise go unnoticed, and helps optimize handover and prioritization workflows.
But even after a sample reaches the lab, work doesn’t necessarily begin right away. q_alizer continues to track the time between arrival and the actual start of testing. Whether the delay is caused by instrument scheduling, setup tasks, or staffing constraints, the system highlights these idle times. With clear metrics and comparisons across teams or test types, labs can take targeted action to reduce non-value-added time.
Pinpointing Bottlenecks in Result Review
Another critical stage in the QC process is result review — a step that often becomes a hidden bottleneck. Whether results are reviewed manually or released automatically, q_alizer measures how long each review takes and where delays build up. It identifies overloads among specific reviewers or sample types and helps labs reallocate capacity so that focus stays on critical deviations rather than routine data.
Illuminating the Final Mile: Sample Release
Once results are reviewed, the final release should follow swiftly — but that’s not always the case. q_alizer tracks the time between review and release, revealing delays linked to unclear responsibilities, missing approvals, or simply high workload. This final transparency enables smoother coordination between QC and QA teams and shortens the time-to-release for entire batches.
Beyond Monitoring: Planning, Deviation Management and More
q_alizer isn’t just a monitoring tool — it’s a strategic cockpit for quality control. Its planning module allows labs to simulate workloads, forecast bottlenecks, and optimize how teams and equipment are deployed. Deviation management becomes data-driven, with early detection and root cause insights built in. KPI dashboards offer instant visibility into lab performance, while benchmarking features allow organizations to see how they stack up against peers in the industry.
LEAN Starts with Visibility
You can’t improve what you don’t see. q_alizer gives pharmaceutical QC teams the insights they need to drive meaningful change — uncovering hidden inefficiencies, accelerating throughput, and enabling faster, data-informed decisions. It connects the dots between data, insight, and action — and delivers measurable returns. In most cases, the ROI is visible within just 3 to 6 months. Learn more: Business Case for QC and QA
Get in contact
Intrigued and ready to learn more about how to better fly your plane?
Cool, the team is waiting to give you a demo of how easy your life will be with q_alizer™!
We’d love to talk with you!
COO
britta.schweinlin@q-alizer.com
044 303 45 56